All You Need to Know About Chemical Defoamer and Its Benefits
All You Need to Know About Chemical Defoamer and Its Benefits
Blog Article
How a Chemical Defoamer Can Enhance Performance in Your Procedures and Procedures
In today's affordable industrial landscape, functional effectiveness is vital, and the role of a chemical defoamer can not be forgotten. By dealing with foam-related obstacles that interfere with processes, defoamers not only assist in smoother procedures yet also add to cost savings and improved item top quality. Their influence extends numerous sectors, making them a crucial consideration for those wanting to enhance performance. Nevertheless, comprehending the certain advantages and applications of defoamers increases crucial inquiries concerning their option and execution. What elements should you consider to maximize their effectiveness in your procedures?
Understanding Chemical Defoamers
Chemical defoamers play a crucial duty in different industrial procedures by properly preventing and reducing foam formation. Frothing can result in operational ineffectiveness, increased manufacturing expenses, and jeopardized product high quality. Defoamers are specialized chemical ingredients designed to interrupt the stability of foam bubbles, thus making it possible for smoother processing and enhanced efficiency across a number of fields, including food and drink, pharmaceuticals, and wastewater therapy.
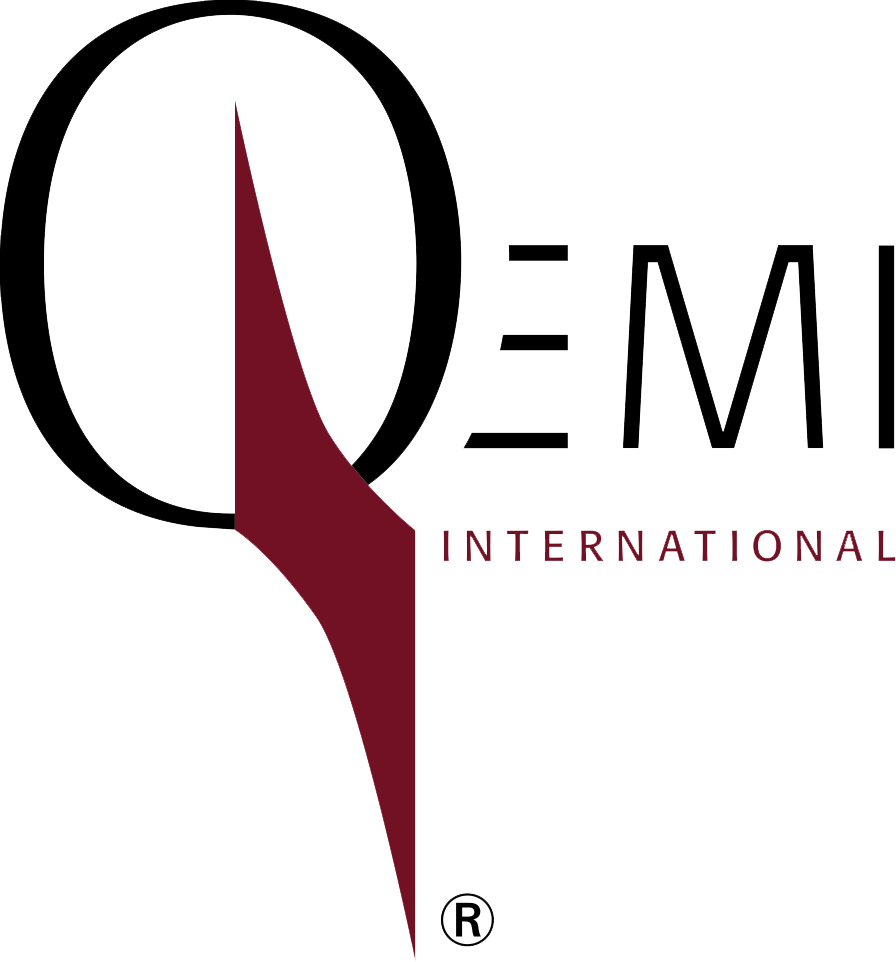
These representatives generally are composed of surfactants, oils, or polymeric compounds that lower the surface area tension of the fluid, facilitating the collapse of foam. The system by which defoamers operate often includes the destabilization of foam frameworks, enabling quicker drain of liquid and the launch of caught air. Various formulations are customized to details applications, thinking about variables such as compatibility with the system, temperature, and the nature of the liquid being dealt with.
Understanding the structure and capability of chemical defoamers is important for choosing the ideal item for an offered application. By enhancing defoamer choice based on process demands, industries can boost functional efficiency, minimize foam-related difficulties, and eventually improve overall productivity.
Benefits of Using Defoamers
Utilizing defoamers can substantially enhance operational effectiveness throughout various markets by properly mitigating foam-related issues. The visibility of foam can interfere with processes, resulting in boosted downtime, minimized performance, and possible top quality degradation in final product. Defoamers help fight these difficulties by breaking down foam structures, thus enabling smoother procedures.
Among the main benefits of utilizing defoamers is the reduction of waste and remodel. By reducing foam formation, defoamers improve the consistency of processes, guaranteeing that materials are used efficiently. This not only decreases functional prices but likewise adds to sustainability efforts by minimizing resource usage.
Additionally, defoamers can boost product quality. In manufacturing settings, extreme foam can result in incongruities in item characteristics, impacting customer satisfaction. By regulating foam degrees, defoamers assist preserve the desired physical properties of items.
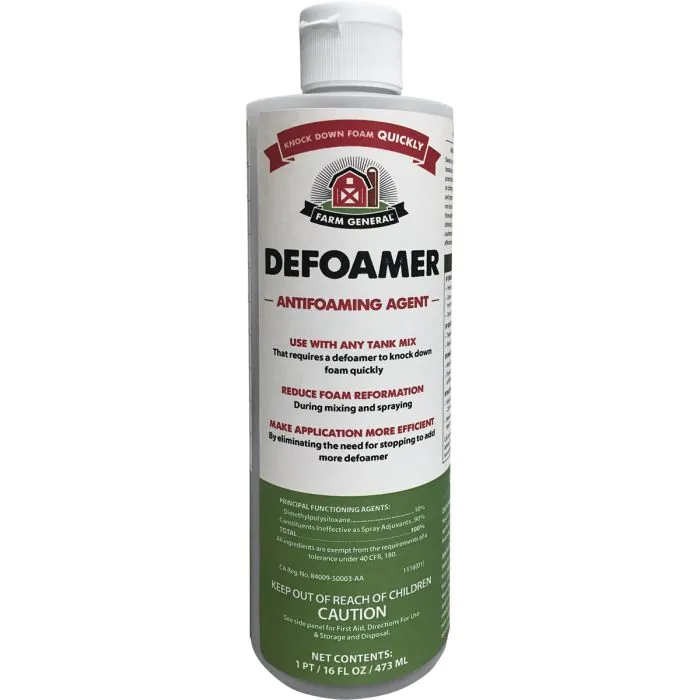
Applications in Various Industries
The effectiveness of defoamers extends across a broad variety of sectors, where their application addresses details foam-related challenges fundamental to every market. In the food and drink sector, defoamers are critical for optimizing production processes, such as developing and milk processing, where extreme foam can hinder flow prices and decrease efficiency. By decreasing foam, these agents enhance product quality and consistency.
In the chemical manufacturing sector, defoamers are employed in processes like paint manufacturing and wastewater treatment. Right here, they prevent foam development that can interfere with blending and different phases, thereby improving the total effectiveness and efficiency of operations.
In pharmaceuticals, defoamers play a vital role in the formulation of fluid drugs, making sure appropriate dosage and stability by controlling foam throughout blending and storage. (Chemical Defoamer)
Additionally, in the agricultural field, defoamers are made use of in chemical formulations to improve application efficiency and lessen waste.
Selecting the Right Defoamer
Choosing the ideal defoamer is critical for accomplishing ideal performance in numerous applications. The choice process need to start with an extensive understanding of the particular concerns available, including the kind of foam existing, the processing problems, and the chemical compatibility with other formulation parts.
Defoamers are formulated from a selection of products, including silicone, mineral oils, and fats. Identifying the appropriate structure is important, as various materials show differing performance in official source diverse atmospheres. Silicone-based defoamers are usually favored in high-temperature applications due to their stability, while organic defoamers may be more ideal for water-based systems.
In addition, take into consideration the defoamer's effect on the last item. Some solutions can modify the visual or functional homes, making it important to pick a defoamer that meets product requirements without endangering top quality.
Examining is one more important action in choosing a defoamer. Small trials can offer valuable insights into the defoamer's efficiency, permitting adjustments prior to major implementation. By thoroughly examining these variables, companies can improve performance and make certain that the defoamer efficiently satisfies their functional demands.
Ideal Practices for Execution
Implementing a defoamer efficiently needs mindful preparation and adherence to ideal techniques to optimize its efficiency. Initially, carry out a comprehensive assessment of the particular application and foam qualities. Understanding the type and source of foam will certainly guide the selection of the most suitable defoamer solution.
Following, develop the optimal dosage (Chemical Defoamer). Start with a small-scale test to identify the minimum efficient concentration, as extreme usage can result in damaging impacts on product top quality or operational effectiveness
Tracking and adjusting the application method is essential; guarantee that the defoamer is introduced at the right factor in the procedure for optimal effect, such as during blending or immediately after foam development.

Furthermore, keep clear communication with all appropriate employees to ensure constant application techniques and to share understandings on performance results.
Final Thought
In conclusion, the usage of chemical defoamers plays an essential duty in enhancing operational effectiveness throughout varied sectors. By properly destabilizing foam, these agents help with quicker drain and air launch, therefore minimizing disruptions look at more info and decreasing expenses. The calculated application of defoamers not just boosts throughput yet additionally ensures consistent item high quality and source optimization. Eventually, the unification of defoamers into commercial processes cultivates integrity and adds to total efficiency enhancement.

In the food and drink industry, defoamers are important for maximizing production processes, such as developing and milk handling, where extreme foam can hinder circulation rates and reduce effectiveness. Silicone-based defoamers are usually favored navigate to this site in high-temperature applications due to their stability, while organic defoamers may be a lot more ideal for water-based systems.
Report this page